Going into the year 2022, one of the leading concerns worldwide is climate change. It is now widely accepted that one of the top contributors to adverse climate change is the burning of fossil fuels – the burning of fossil fuels such as coal or oil leads to the release of large amounts of carbon dioxide into the air, trapping heat in our atmosphere and causing global warming.
Plastics, the material ubiquitously found in products ranging from grocery bags to car bumpers and even clothes, are traditionally made from synthetic polymers derived from petroleum. The building blocks of these polymers are either obtained directly from crude oil refining or synthesized from refining products. It is estimated that plastic manufacturing processes consume 8–10% of the global oil supply, with this number set to double by 2040.
The production of petrochemicals and traditional plastics is still wholly reliant on oil, and this non-renewable resource is rapidly being depleted from planet Earth. The problem with plastics is therefore multifold: standard plastic production must eventually cease due to dwindling resources; this production method damages our ecosystem, and many plastic products are not reusable, creating extraordinary amounts of waste and causing further damage through not being disposed of/recycled properly.
The average person can reduce their ‘ecological footprint’ and help the environment by using single-use and disposable plastics, reducing packaging waste, and recycling responsibly. Manufacturers can equally improve their ‘ecological footprint’ by choosing an alternative source to petroleum when developing plastics, which entails selecting biopolymers instead of their synthetic counterparts.
Although “biopolymers” is sometimes used to describe biodegradable or biocompatible polymers (regardless of origin), in this blog we use this term to refer to only bio-derived polymers, i.e. polymers created from biomass. They are generated from renewable sources, which also fix CO2 from the atmosphere and decrease greenhouse gas emissions. Many biopolymers are also biodegradable, providing more flexibility in disposing of products made with them and enabling recycling.
Types of biopolymers
There are three major classes of biopolymers, separated by their source and production method:
- Class A: Natural polymers obtained directly from biomass, such as starch, cellulose, proteins, amino acids, and derivatives
- Class B: Polymers that are bio-synthesized using microorganisms and plants, or prepared directly from monomers that are predominantly bio-synthesized, such as polyhydroxyalkanoates (PHAs) and polylactic acid (PLA)
- Class C: Conventionally oil-based polymers prepared from alternative bio-sourced monomers, such as polyethylene and polyethylene terephthalate (PET)
Each class of biopolymer is suited to different commercial applications, whether it be packaging materials, agriculture, or biomaterials for surgery:
- Class A and B polymers are all biodegradable and are nearly all bio-based, but have inferior properties compared with oil-based plastics, so are often used in combination with reinforcing fillers or impact modifiers
- Class C polymers are structurally similar to oil-based plastics, but are mostly not biodegradable and thus share the same disposal and recycling issues
The challenge to the increased uptake of biopolymers is cost. Initiatives aimed at improving fermentation yield and efficiency or integrating the production of biopolymers into food manufacturing plants or facilities with organic waste streams are attempting to take the edge off the high manufacturing costs, but this remains a key obstacle.
What are biopolymers currently used for?
Commercial bioplastics have been mainly used in packaging (Table 1). Starch and PLA are the most manufactured bioplastics, most likely due to their lower costs. PHAs, on the other hand, have high production costs and thus have been made in much lower quantities.
Table 1. Production and applications of top commercial biopolymers
It’s the ‘cool’ thing: Coca-Cola’s PlantBottle™
Sustainable innovation in biopolymers has been developing behind the scenes for decades, but these advances are not often newsworthy or publicly seen until top companies announce a new product.
In the summer of 2015, the Coca-Cola Company unveiled its PlantBottle™ packaging - the world’s first plastic bottle made entirely from renewable resources. These bottles look, function, and recycle the same as bottles made from traditional plastic but have a significantly smaller impact on the planet by not touching petroleum. Announcements like this are encouraging for the continued development of biopolymers and their adoption in mainstream products worldwide.
Misconceptions vs facts about biopolymers
Public perception of biopolymers is also important for the wider implementation of these products; while the great benefits of these sustainable alternatives to traditional plastics are generally acknowledged, they have also been subject to criticism. Some of these criticisms have understandably arisen from misconceptions or confusion but others have come out of left field – Table 2 holds our opinions on some of the most frequently discussed topics.
Table 2. Misconceptions vs facts about biopolymers.
PBAT = polybutylene adipate terephthalate; PBS = polybutylene succinate; PLA = polylactic acid.
The biopolymer research landscape
Biopolymer research has been trending in recent years and was chosen as one of the top ten emerging technologies of the year 2019. Research and innovation leading up to this have been ongoing over the last two decades, as seen in the CAS Content Collection™ (Figure 1), constantly responding to fluctuations in oil prices and the general drive to increase sustainability and tackle climate change. The volumes of both journal publications and patents began to initially rise slowly but accelerated at a similar same pace from about 2009. Around 2014, the growth in patent publication volume slowed down considerably in contrast with the strong increase in journal publication numbers up to 2020.
As biopolymers are mainly developed as renewable alternatives to fossil-based plastics, substantial rises in the latter’s prices would increase biopolymers’ competitiveness, alongside boosting enthusiasm and confidence among researchers and inventors. Plastic prices are tightly linked to oil prices, which experienced substantial growth since the mid-2000s and an unprecedented sharp peak in 2008, which may potentially explain the inflection point, particularly visible in the patent publication number curve at around 2008. Oil prices plummeted after 2014, making biopolymers relatively more costly again, thus presumably discouraging inventors and causing the patent publication volume to level off in the exact same year.
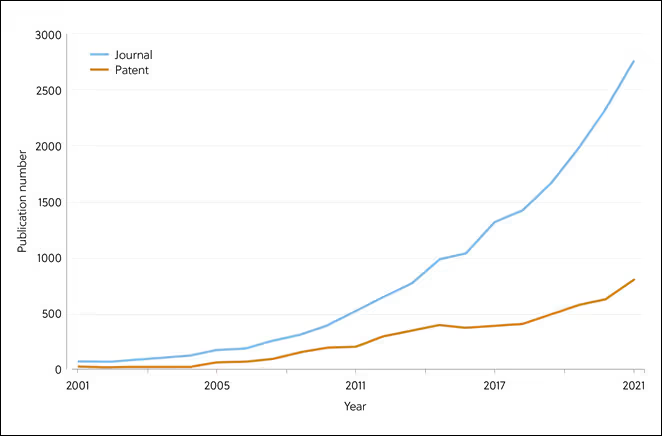
Read our CAS Insights Report to find out more about the advantages, limitations, and popularity of the different classes of biopolymers, and how the research and development interest in these traditional plastic alternatives has changed over the last two decades.